Warehousing Industry Costs? What can we do?
Nov 03, 2024 | ondemand_user
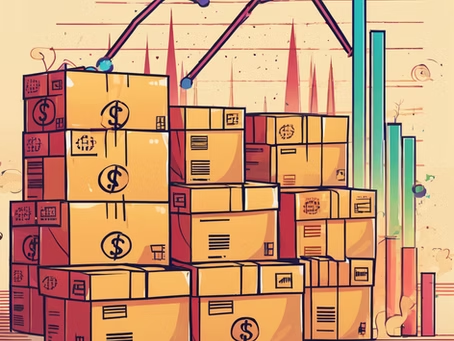
Understanding Warehousing Industry Costs: Key Factors and Strategies for Efficiency
The warehousing industry is a vital component of supply chain management, serving as the bridge between production and distribution. As businesses strive to optimize their operations, understanding the costs associated with warehousing becomes crucial. Here’s a breakdown of the key factors influencing warehousing costs and strategies to enhance efficiency.
Key Cost Factors in Warehousing
- Real Estate Expenses
- Rent or Purchase Costs: The location of a warehouse significantly impacts rental or purchase prices. Warehouses situated near major transportation hubs often incur higher costs but provide logistical advantages.
- Utilities and Maintenance: Ongoing expenses such as electricity, water, and facility maintenance must be considered. Efficient energy use and regular maintenance can mitigate these costs.
- Labor Costs
- Wages and Benefits: Labor is one of the largest expenses in warehousing. The cost of hiring, training, and retaining staff can vary widely based on location and job requirements.
- Overtime and Productivity: Fluctuations in demand can lead to increased overtime costs. Implementing technology and automation can help optimize labor productivity and reduce reliance on overtime.
- Inventory Management
- Holding Costs: These include costs associated with storing unsold goods, such as insurance, taxes, and spoilage. Efficient inventory management strategies can minimize holding costs.
- Shrinkage: Losses due to theft, damage, or mismanagement can add significant expenses. Investing in security and effective inventory tracking can reduce shrinkage rates.
- Technology and Equipment
- Initial Investment: Automated systems, warehouse management software (WMS), and equipment like forklifts and shelving units require significant initial investment.
- Maintenance and Upgrades: Ongoing costs for maintenance and periodic upgrades of technology and equipment must be factored into the budget.
- Transportation Costs
- Inbound and Outbound Logistics: Transportation expenses related to moving goods to and from the warehouse can greatly influence overall warehousing costs. Efficient route planning and consolidation can help minimize these costs.
Strategies for Reducing Warehousing Costs
- Optimize Warehouse Layout
- Efficient layout design can reduce travel time for staff and improve workflow. Implementing a systematic approach to product placement can streamline operations.
- Implement Technology Solutions
- Utilizing warehouse management systems (WMS) can enhance inventory accuracy, improve order fulfillment speed, and reduce labor costs through better task allocation.
- Adopt Automation
- Automated solutions such as robotics and conveyor systems can enhance efficiency and reduce labor dependency. While the initial investment is high, the long-term savings often outweigh costs.
- Enhance Training Programs
- Investing in employee training ensures staff are skilled in using technology and following best practices, leading to improved efficiency and reduced errors.
- Conduct Regular Audits
- Periodic reviews of operations can identify inefficiencies and areas for cost reduction. Regular audits of inventory and labor can highlight opportunities for improvement.
Conclusion
Understanding and managing warehousing costs is essential for businesses seeking to enhance their supply chain efficiency. All of these factors make it an overwhelming task to some to find the right balance and get down to a true Cost of Goods Sold (COGS). Let us help take some of the guess work out of this but using our years of experience and market leverage to provide a more easily predicted transactional rate for your warehousing operations.